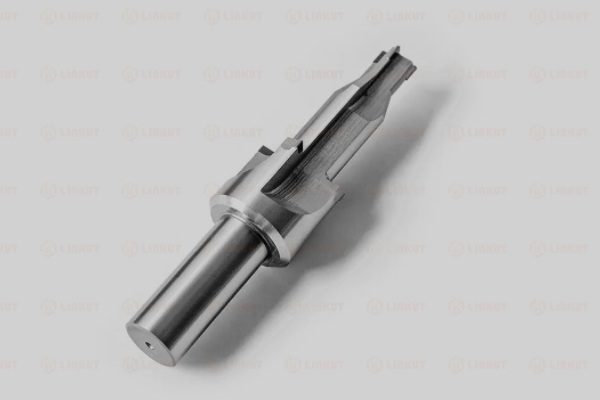
PCD Reamers
Features:
Advantages of LINKUT PCD Reamers are:
Longer tool life;Fewer tool changes;Tool costs significantly reduced;
Higher machining efficiency;Higher cutting speed;
Better surface finish quality;Improved workpiece quality;
Lower machine downtime.
Reaming with a PCD tool allows the user to ream holes faster, to tighter tolerances and produce cleaner-edge holes than is possible with carbide or HSS tooling.
In addition, by producing cleaner edges, a PCD reamer can reduce, or even eliminate, the need for secondary finishing operations such as deburring, thereby lowering overall production costs.
PCD reamers provide consistent results for a longer time than their traditional counterparts, because production does not have to be periodically interrupted to change worn tools.
For a manufacturer engaged in steady production, a carbide tool might last a few days to a week, while a PCD tool could last for months.
Experience shows that during production reaming, the extended tool life a PCD reamer provides, along with reduced secondary operations, typically results in a cost per hole that equals 20 percent of the cost per hole when a carbide reamer is used.
In addition to high-volume-production facilities, job shops can achieve savings with PCD reamers. The reason is because a tool’s effective life is measured over the total number of holes reamed, regardless of the number of separate projects involved.
PCD reamers are used in cutting aluminum, brass, copper, graphite and other materials like wood, plastic and carbon-fiber-reinforced polymer.
LINKUT PCD reamers have stable boring drilling roughness, surface finish, and size control performance. Meanwhile, they are available to ensure the complex shape with excellent concentricity, straightness accuracy, and bore location.
-
PCD Countersinks
Details -
EDM Cuttable Silicon Polycrystalline Dia
Details -
CVD Diamond for Thermal Management&&Opti
Details -
PCD Blanks
Details